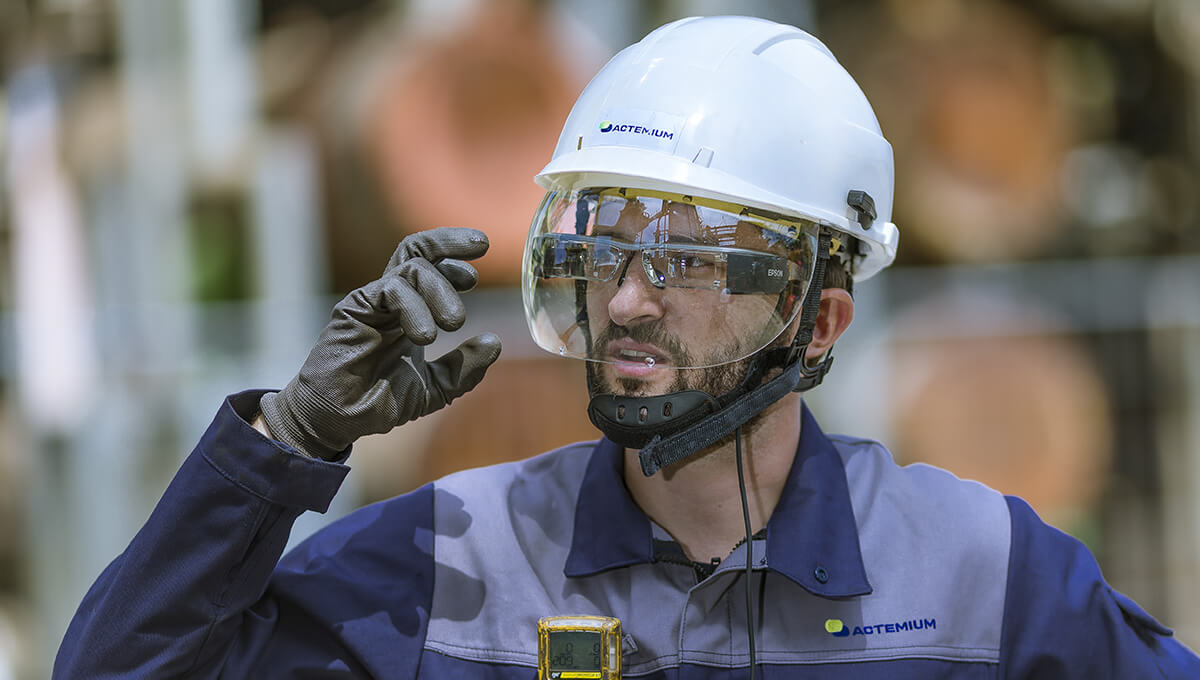
© Raphaël Soret
Actemium war beteiligt an der Einrichtung einer Fernwirkzentrale (Remote Control Center) für Air Liquide in der Nähe von Lyon, von der aus künftig alle Produktionsanlagen in Frankreich und bald weltweit überwacht und gesteuert werden.
Seit Ende Januar 2017 befindet sich die Steuerungszentrale von Air Liquide in Saint-Priest, einem Vorort von Lyon. Von diesem Remote Control Center aus soll die Industriegasproduktion in zweiundzwanzig Betrieben des Konzerns in ganz Frankreich gesteuert werden. Bei diesem Projekt zur digitalen Transformation der Air Liquide-Gruppe namens „Connect“ geht es um Datenerfassung, Big Data und neue Technologien, die das Kernstück der Fabrik der Zukunft bilden.
Alle Daten werden zentral erfasst und mithilfe eigens dafür entwickelter Algorithmen analysiert. Daraus lässt sich die Häufigkeit von Ausfällen ablesen, um Teile rechtzeitig auszuwechseln.
Anpassung des Energieverbrauchs
„Hauptziel für Air Liquide ist die Optimierung der Produktion, wobei die hohe Energieintensität bei der Herstellung von Industriegasen einen wichtigen Faktor darstellt“, erläutert Rodolphe Letondor, zuständiger Projektleiter bei Actemium (VINCI Energies). „Ziel ist daher eine präzise Steuerung der Anlagen“.
Dank der erfassten Ist-Daten sowie der historischen Produktionsdaten von 400 Betrieben seit 15 Jahren kann von der Fernwirkzentrale aus festgestellt werden, ob der Energiekonsum eines Standorts dem Soll entspricht, um ggf. erforderliche Regelungen vorzunehmen.
Die Maßnahmen zur Optimierung beschränken sich jedoch nicht nur auf den Energieverbrauch. Mit einer Gesamtübersicht über alle Betriebe und den jeweiligen Kundenbedarf erfolgt über das Remote Control Center eine nachfragegerechte Steuerung der Produktion von Sauerstoff, Wasserstoff, Stickstoff und Argon. Auch das An- und Abschalten einer Anlage kann ferngesteuert erfolgen.
Optimierte Anlagenverfügbarkeit
Ein weiteres Ziel von Air Liquide besteht in einer zuverlässigeren Prozesstechnik durch prädiktive Wartung. Die erfassten Betriebsdaten werden zur Erkennung erster Anzeichen einer Panne oder Störung analysiert. „Alle Daten sowie die Art der aufgetretenen Ausfälle und Störungen werden zentral erfasst und mithilfe eigens dafür entwickelter Algorithmen analysiert. Daraus lässt sich die Häufigkeit von Ausfällen ablesen, um Teile rechtzeitig auszuwechseln und Problemen vorzubeugen“, so Rodolphe Letondor.
Desgleichen wird durch neue Technologien auch der Inspektions- und Wartungsaufwand vereinfacht: Touchscreens, Datenbrillen, 3D-Scans. „Bei einer Inspektionstour kann auf Server zugegriffen werden, um beispielsweise Pläne abzurufen oder Informationen in die Datenbrille einzublenden. Allein die Tatsache, diese Informationen nicht umständlich suchen zu müssen, ist eine enorme Arbeitserleichterung“, führt er aus.
Im Augenblick sind nur vier Betriebe miteinander vernetzt. Bis Ende 2017 sollen alle französischen Werke eingebunden sein. In einer zweiten Welle wird das System dann auch auf die Produktionsstätten außerhalb Frankreichs ausgedehnt.
03/07/2017