A low- CO₂ plasterboard factory is under construction in Norway
Reading time: 3 min
Actemium Electro has been tasked with the electrification of a Saint‑Gobain plasterboard factory previously powered by natural gas. The outcome will be less energy consumption, fewer emissions – and more production.
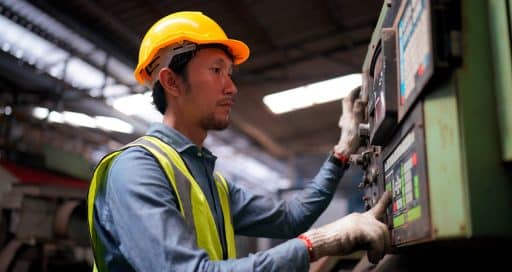
The Gyproc Saint Gobain factory in Fredrikstad, Norway, will reduce its carbon footprint by making its production all-electric.
The green transition in manufacturing involves a radical transformation of processes. In Norway, Saint-Gobain Gyproc is currently transforming its plant in Fredrikstad, a port town in the south of the country, into a low- CO₂ plasterboard production facility.
When works are completed in 2023, the factory will reduce its yearly carbon dioxide emissions by more than 23,000 tonnes and its energy consumption by 30% per unit produced. At the same time, its production capacity will increase by 40%.
The electrification of the factory is what makes these performance gains possible. Electrical power will replace the natural gas currently used for burning and for drying the gypsum boards.
To provide enough electricity to a factory that consumes around 240 GWh of energy per year, equivalent to the consumption of around 20,000 Norwegians, two new electric substations will be built, with a total of seven transformers.
“The timescale is tight. All the work to replace the equipment must be completed in just five weeks.”
For Saint‑Gobain, this pilot project is strategic in terms of applying ecological transition to around 70 other facilities of this type that the group operates worldwide.
Tight timescale
Actemium Electro has been appointed to electrify the factory. “Actemium Electro Sarpsborg was assigned the high-voltage component of the project in partnership with Omexom”, says Jon-Ottar Ellefsen, CEO of Actemium Electro AS. “We are also working with Krogseth AS, our HVAC [heating, ventilation and air conditioning] partner”.
The business unit is responsible for all high- and low-voltage installations on site, the main cabinets, and all cabling and electrical infrastructure for the project. Jon-Ottar Ellefsen says, “We are also installing all the lighting, fire detection equipment, cabling for the motors and frequency converters, plus instrumentation and monitoring”.
The main challenge will be meeting the deadlines – “The timescale is tight”, he adds. “Over the winter, we will be removing all the equipment and cabling from the old factory before installing new equipment suitable for electrification of the site. This work must be completed in just five weeks”.
Actemium hopes to capitalise on this experience to help transform more of the Saint‑Gobain group’s plasterboard factories around the world.
16/03/2023