Industry: from lean management to sustainable manufacturing
Reading time: 5 min
Under pressure from increasingly stringent regulation, manufacturers are having to overhaul their production models to make them more sustainable. Here, we look at some examples from the construction sector.
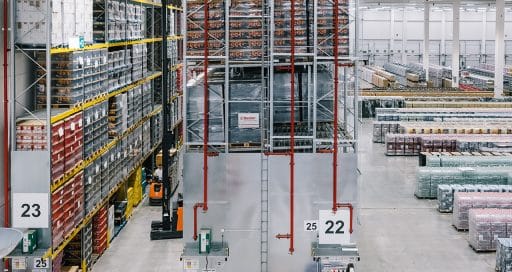
The six R’s of sustainable manufacturing: reduce, reuse, recycle, recover, redesign and remanufacture.
Since the 1950s, lean management has emerged as “the” method for continuous improvement in competitiveness. Developed by Toyota in Japan, this approach aims to adapt business methods (processes, practices, skills) as closely as possible to customer needs (quality, quantity, timescales). In other words, lean management seeks to identify then reduce, if not eliminate, everything that costs money or time without adding value.
Although these initial aims differed from those prioritised in the sustainable development concept, lean management quickly converged with the latter’s imperatives, particularly in terms of energy efficiency and waste reduction – these are the famous 3 R’s: Reduce, Reuse, Recycle.
But against a backdrop of accelerated climate heating, manufacturers are being spurred into action by increasingly strict environmental legislation and must now move from lean manufacturing to sustainable manufacturing. The latter can be summed up in six key words – the six R’s: Reduce, Reuse, Recycle, Recover, Redesign and Remanufacture. In other words, monitoring a product throughout its life cycle from a circular economy perspective.
Integrating low tech
For example, take the construction sector – a major greenhouse gas emitter, which will have to go all out to transform itself quickly. “The new RE2020 regulation significantly increased environmental and sustainability requirements. The entire stakeholder chain has to comply with these”, notes Stéphane Bretin, Maintenance and Service Manager at Building Solutions, which combines the VINCI Energies’ Engineering & Contracting, Multi-technology Maintenance and Facility Management businesses.
“We must incorporate the idea of low tech”, he continues. “with two priorities: not only reducing the impact of a product across its entire life cycle, but also adapting to climate change, with higher winds, flooding and more intense heatwaves”.
For Stéphane Bretin, “This can translate into a functional saving, for example by seeking to satisfy occupants’ comfort needs while doing away with climate control systems. But in this case, you first have to reconsider the overall design of the building before you can turn to alternative solutions such as increasing mechanical ventilation”.
Circular solutions
Even if the solution is obvious and the intention clearly stated, the road is still a long one… According to a study by Capgemini Research Institute, only 11% of manufacturers have made a concrete commitment to sustainable manufacturing, and less than 40% expect to reduce their use of natural resources over the next decade.*
“We must incorporate the idea of low tech, with two priorities: reducing the impact of a product across its entire life cycle and adapting to climate change”
VINCI Energies is one group doing its part to accelerate the movement.
This solution can be costly, however. Removing materials with the intention of reusing them requires specific expertise and additional labour time. “But by managing the entire process internally without intermediaries, we are optimising the economic model for this type of approach”, says Stéphane Bretin.
Accordingly, 600 kilos of ventilation ducts removed from the former H&M store on the Champs Élysées in Paris were recently reconditioned and stored for reuse on another project. Similarly, in the suburbs of Paris, a kilometre of cable channels extracted from a site in Pantin will soon be reused in Levallois Perret.
Change management
Another initiative, this time from Actemium Laxou, one of the VINCI Energies business units specialised in industrial processes, involves using recycled shipping containers remade into shelters for the creation of biomethane injection stations.
“In doing this over the last three years, the Actemium Laxou team has saved 90 tonnes of CO2 per container. This concept is not just sustainable, but also profitable, as a recycled container costs around 20% less than a new one”, says Marcos-Raul Salido-Portugal, Sustainability Project Manager at VINCI Energies.
It would seem that industry is no longer content to merely talk about ecological transformation. On the front line, the construction sector has little choice. “The tertiary decree** coming into force in September 2022 will considerably increase the requirements, with targets of a 40% reduction in energy expenditure by 2030 and a 60% reduction by 2050”, says Stéphane Bretin. The Building Solutions Maintenance and Service Manager advocates actively supporting change, as with the internal training providdiplômes de fiertéed by the VINCI Energies Building Solutions Institute.
* Capgemini research institute, “Sustainability in Manufacturing Operations” survey carried out in February–March 2021
** Dispositif Eco Efficacité Tertiaire (DEET) – Tertiary Eco Efficiency Scheme
14/12/2022