La industria 4.0 ante el reto de la personalización masiva
Tiempo de lectura : 5 min
La industria 4.0 anuncia una revolución de los procesos, una revolución que se está produciendo principalmente en el sector automovilístico. Algunos actores clave están a la vanguardia en el tema, como el grupo Stellantis, para el que trabaja Actemium (VINCI Energies). El reto: combinar personalización y agilidad.
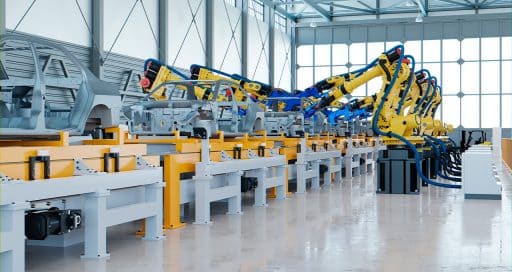
La fábrica 4.0 implica una mayor flexibilidad en los procesos de producción y, por tanto, una mayor automatización.
El modelo de producción masiva basado en el principio “un producto, una fábrica, un país” es cosa del pasado. Hoy en día, los nuevos modelos industriales deben conciliar lo inconciliable, o al menos lo que parece serlo: producir de forma estable con el máximo aprovechamiento de la herramienta industrial, y al mismo tiempo suministrar un gran número de productos distintos y más personalizados, y todo ello dentro de una cadena de suministro mundial.
El reto de la fábrica 4.0 es crear un sistema industrial flexible, automatizado y resiliente. Para responder a este desafío, es necesario recurrir a un nuevo concepto: la personalización masiva, que implica una mayor variabilidad en los procesos de producción y, por tanto, una mayor automatización.
En este sentido, la industria automovilística constituye un interesante caso de uso. “La creciente diversidad de los productos y su personalización (color, rueda, llanta, acabados, cuero, asiento calefactable…) obliga a revisar la organización de las cadenas de producción”, señala Patrick Bénard, director regional de Industrie Nord Est en VINCI Energies, que trabaja para el grupo Stellantis (Peugeot, Citroën, DS, Opel, Vauxhall, Fiat, Chrysler, Abarth, Lancia, Alfa Romeo, Maserati, Jeep, Ram y Dodge).
Crear un sistema industrial flexible, automatizado y resiliente. Este es el desafío de la fábrica 4.0.
Hasta ahora, las fábricas se basaban en el principio de la línea de montaje, donde las tareas se dividen en distintas fases. En cada una de ellas, los equipos son fijos y un sistema logístico de borde de línea proporciona todos los componentes necesarios para la fabricación.
Nuevo proceso
Pero este modelo de producción solo permite fabricar productos parecidos con algunas variaciones, y no productos realmente distintos. ¿Cómo evolucionar, entonces? “En 2014, la fábrica PSA de Mulhouse (ahora Stellantis Mulhouse) fue una de las primeras plantas europeas en adoptar un nuevo proceso industrial”, manifiesta Patrick Bénard.
¿El principio? “Dejar de situar las piezas de antemano en borde de línea y transportar los kits de montaje según las necesidades gracias a AGV (vehículos de guiado automático)“, explica. Estos sistemas de plataformas móviles se desplazan automáticamente del centro logístico a las estaciones de trabajo.
Pero este procedimiento industrial requiere una logística extremadamente compleja, con batallones de AGV que tienen que entregar en la estación adecuada y el momento preciso el lote correcto de componentes necesarios para fabricar un producto.
La solución: “una gestión muy precisa del tráfico de AGV”. En este sentido, Actemium Mulhouse diseñó para Stellantis un sistema de supervisión ad hoc que se implementó rápidamente en las demás fábricas de Francia y más tarde en países como España o Eslovaquia.
Desde 2012, “Actemium ha instalado más de 1.500 AGV en las fábricas de Stellantis”, puntualiza Patrick Bénard. Según el director regional de VINCI Energies, la logística cada vez más automatizada está llamada a convertirse en un elemento cada vez más importante de la producción industrial.
Mayor flexibilidad
Este tipo de proceso presenta múltiples ventajas. “En primer lugar, permite reducir el tamaño de las fábricas, ya que pueden producirse diferentes modelos y variaciones de productos en una misma línea de montaje que se adapta según las necesidades”, explica Patrick Bénard.
Otra ventaja de “este sistema de flujo único” es la posibilidad de instalar de uno a tres equipos distintos en la misma línea, según los productos que se vayan a fabricar. “Esta flexibilidad es aún mayor cuando se utilizan las mismas plataformas de vehículos para diferentes modelos o marcas”, añade.
Para el director regional de VINCI Energies, Stellantis es uno de los pocos grupos que han sabido replantearse su proceso de fabricación cuando las cosas iban bien. “Esta anticipación ha sido beneficiosa para el grupo”, señala. “A raíz del aumento de su productividad, presenta un margen operativo actual del 14% en el primer semestre de 2022, uno de los más elevados del sector”.
16/03/2023