Flexiplant met de l’agilité dans les lignes de production
Temps de lecture : 6 min
Actemium Saint-Etienne Process Solutions a créé un système clé en main, automatique et évolutif, destiné à améliorer la performance industrielle des sites de production de poudres dédiées à la construction.
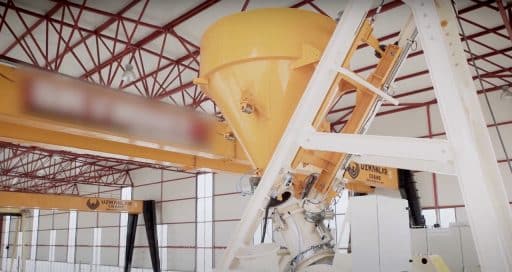
La ligne de production conçue par Actemium Saint-Etienne Process Solutions a été brevetée dès 2015.
Dans un contexte de triple crise, économique, climatique et énergétique, le monde industriel, particulièrement gourmand en énergies fossiles et émetteur de CO2, est enjoint à revoir ses modèles. Pas si simple… Pour les sites industriels, caractérisés par la lourdeur structurelle de leurs installations et la rigidité de leurs cycles de production, les freins à la transformation sont nombreux.
Mais les leviers d’action, eux non plus, ne manquent pas, tant dans les registres techniques qu’organisationnels. Intervenir sur certains schémas de production, par exemple, peut suffire à améliorer l’efficience économique et énergétique de certains sites.
C’est le pari relevé par Actemium Saint-Etienne Process Solutions, entreprise de VINCI Energies spécialisée depuis 1991 dans l’industrialisation des procédés de production mettant en œuvre des produits pulvérulents, granulés ou pâteux, principalement pour l’industrie de la chimie de la construction (colles, enduits, chapes…).
En 2015, cette société de 35 salariés a breveté une ligne de production innovante, baptisée Flexiplant, permettant aux sites industriels de stockage, dosage, mélange et ensachage de poudres d’améliorer significativement leur modèle économique et leur impact environnemental.
Vertical ou horizontal
« Aujourd’hui, les entreprises intégrant des installations de mélange de produits hautement formulés doivent choisir entre deux types d’unités de production, verticale ou horizontale, qui présentent chacune des avantages et des inconvénients », explique Nicolas Genevrier, ingénieur commercial chez Actemium Saint-Etienne Process Solutions.
Les installations verticales garantissent fiabilité et capacité de production, avec en outre un coût de fonctionnement raisonnable et une moindre maintenance. En revanche, elles appellent un investissement initial très élevé et doivent répondre aux exigences administratives de plus en plus drastiques imposées par les plans d’urbanisme locaux et contraintes par la nature sismique des sols.
Un investissement initial 25 % moins élevé pour un coût de fonctionnement réduit de 40 %.
En cause : la taille et la masse de la structure métallique supportant les silos de stockage de matières premières, dont la hauteur atteint généralement 40 m. Autre inconvénient des systèmes verticaux, leur manque de flexibilité et d’évolutivité. A moins que l’extension ait été anticipée lors de la phase de conception et de dimensionnement de l’installation, il est très difficile d’ajouter des silos supplémentaires de charges, des trémies d’additifs, ou une nouvelle ligne de mélange complète.
Les modèles horizontaux, eux, représentent des investissements moindres, pour un coût d’exploitation plus élevé. Leurs capacités de production sont plus limitées et ils présentent des risques de contamination croisée occasionnée par les systèmes de convoyage, notamment pneumatiques.
Le meilleur des deux systèmes
Avec Flexiplant, Actemium Saint-Etienne Process Solutions a choisi d’emprunter aux deux systèmes existants pour en conjuguer les avantages respectifs en laissant de côté les inconvénients. Le système combine ainsi un procédé horizontal, associé à un carrousel proposant trois stations de dosage en simultané pour une meilleure capacité de production et un convoyage mécanique à l’aide d’un skip*, limitant la consommation énergétique et la contamination entre formules.
La hauteur maximale de la ligne varie selon les besoins d’utilisation de 9 à 12 m. L’encombrement global de la ligne lui permet de s’intégrer facilement dans la plupart des entrepôts existants. Il est en outre possible d’y greffer à tout moment, sans arrêt de production, de nouveaux modules ou de nouvelles stations, d’agrandir ou d’adapter certains équipements pour répondre aux évolutions de la production.
Zéro contamination, précision de dosage, évolutivité des installations… Et ça n’est pas tout, insiste-t-on chez Actemium Saint-Etienne Process Solutions. « L’investissement initial requis par Flexiplant est 25 % moins élevé qu’avec une structure verticale. Quant au coût de fonctionnement, il est de 40 % inférieur à celui d’une structure horizontale classique. Ce gain économique étant lui-même imputable à une diminution sensible de la consommation énergétique (vingt fois moins qu’un système horizontal et cinq fois moins qu’un modèle vertical) », détaille Nicolas Genevrier.
Brevetée en 2015, Flexiplant est aujourd’hui présente en France, au Chili, en Australie. La ligne a également été retenue par Sika, l’un des principaux acteurs mondiaux de la chimie de la construction, pour intégrer un deuxième site de production à Boisbriand, près de Montréal (Canada).
« Nous réalisons une grosse partie de notre activité à l’international, avec des contrats un peu partout dans le monde. Flexiplant s’inscrit dans ce schéma d’ouverture. Il s’agit pour nous de projets clé en main d’une valeur de 1,5 à 5 millions d’euros et nous pensons pouvoir tabler sur un potentiel d’une petite dizaine de projets par an », ajoute Nicolas Genevrier.
*Un skip est une installation servant à la montée de charges en vrac, généralement pondéreuses, à l’aide de bennes tirées par un treuil et qui se vidangent par gravité.
21/04/2023