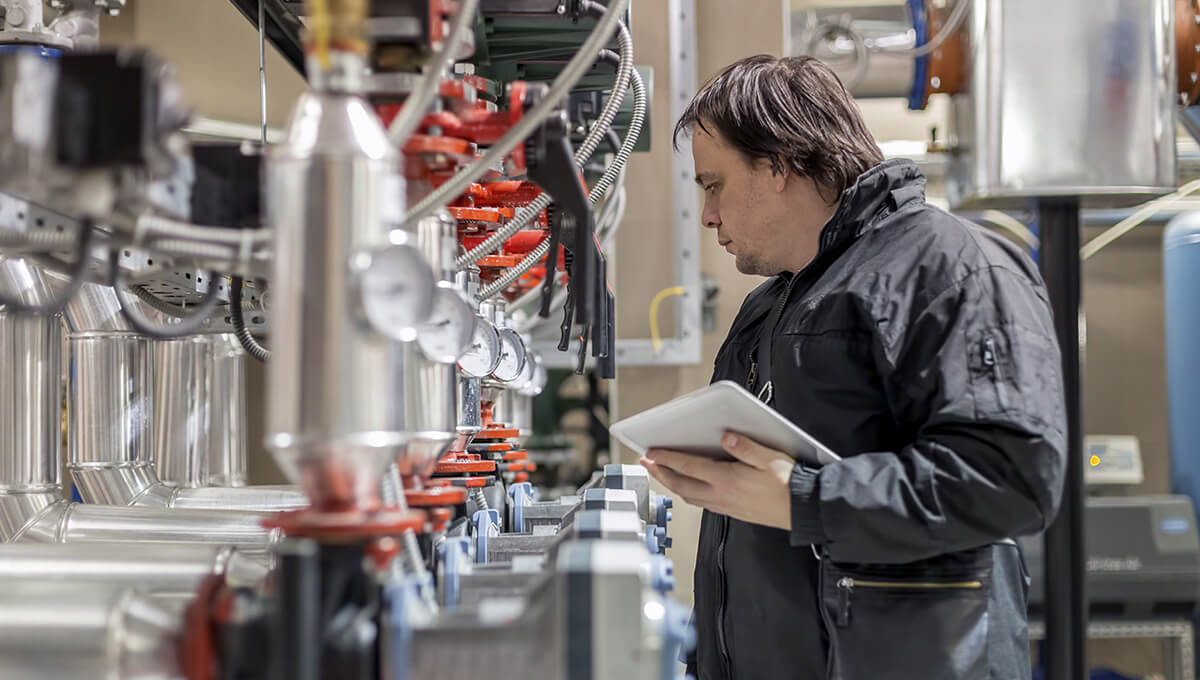
© nimis69/iStock/Thinkstock
Capteurs, données et analyse statistique font partie intégrante des outils à disposition des industriels afin d’anticiper les pannes et d’améliorer les performances.
En se basant sur l’analyse des données fournies par des capteurs installés sur les lignes de production, la maintenance prédictive permet de mesurer les conditions d’utilisation des pièces, en temps réel et en continu. L’avantage ? Tout simplement prévenir les pannes avant qu’elles ne surviennent et changer les pièces avant qu’il ne soit trop tard.
Avec l’IoT (Internet of Things), l’analyse de données passe à un niveau supérieur. « Nous utilisons ces datas comme un « aperçu » afin de prévoir les problèmes et donc les pannes ou besoins en maintenance », indique Joris De Veirman, Branch Manager Industry Software Solutions chez Axians. En se basant sur les données de production et maintenance, cette analyse des données permet d’identifier les causes déclenchant un problème récurrent, et donc de définir des modèles prédictifs.
IT et OT
Chez VINCI Energies, la technologie de l’IoT dans l’industrie combine les expertises d’Actemium et d’Axians, la première étant en charge de la conception des procédés et des installations, et la seconde de la partie digitale. « Entre les lignes de production et les serveurs informatiques, il existe ce lieu commun où nos deux marques travaillent à l’identique, qui est celui de l’analyse de l’information, des données », détaille Aleksandar Maksimovic, directeur technique de la maintenance chez Actemium.
« Le bon rendement financier du matériel de l’IoT nous permet de poser des capteurs et des actionneurs dans les lignes de production pendant la validation de principe, pour envoyer ensuite les données par Internet à des serveurs hors site, où elles seront traitées, ajoute-t-il. Nous avons par exemple travaillé avec l’un de nos clients et des spécialistes de solutions prédictives sur une problématique d’encrassement d’un compresseur sur une ligne de production. Nous avons recherché les principaux facteurs qui influencent cet encrassement, avec comme objectif de limiter les arrêts et redémarrages de l’installation pour optimiser son rendement technique et financier. »
« Avec l’IoT, le risque principal est que l’un des concurrents ait accès à des données confidentielles, comme des techniques de fabrication particulières. »
Qui dit IoT dit sécurité du réseau. Une usine utilise un réseau IT (information technology, couvrant notamment les communications) et un réseau OT (operationnal technology, réseau interne à l’usine), qui travaillent de plus en plus ensemble. Des capteurs mesurent par exemple la quantité de matériaux nécessaires à la fabrication. Lorsque le stock atteint un seuil critique, ces matériaux sont commandés automatiquement, et cela résulte d’une communication de l’OT vers l’IT.
« Puisque les deux convergent et travaillent ensemble, ils doivent être sécurisés, alerte Joris De Veirman. Sans compter que de plus en plus d’objets connectés sont installés dans les usines, mais la plupart des industriels ne sont pas conscients que certaines informations sont envoyées via l’IT. Le risque principal est que l’un des concurrents ait accès à des données confidentielles, comme des techniques de fabrication particulières. » Un point de vigilance à part entière.
16/05/2017